Residential construction often includes several different types of concrete projects. From driveways and sidewalks to foundations and staircases, your contractors will encounter several different processes that all have different standards. And if they’re not prepared, they’re likely to create some of the most common issues in residential concrete work.
But these issues can be avoided with the right knowledge and preparation. The six most common problems come back to one major mistake in almost every case. And if you can get this concept right, the science behind concrete will work for you instead of against you.
What Are the Most Common Issues in Residential Concrete Work?
The most common issues in residential concrete work are cracking, scaling, blisters, popouts, dusting, and discoloration. The causes of these problems typically include slow concrete pour, incorrect water-cement ratios, poorly designed control joints, lack of temperature control, premature finishing, and inadequate air entrainment.
Cracking
One of the most common issues in residential concrete work is cracking. This issue typically stems back to drying shrinkage or the effects of extreme temperatures. Water-to-cement ratios could be off balance, or the concrete might have been poured in temperatures that were too hot or too cold, leading to weakening in the concrete’s tensile strength.
Scaling
When surface mortar breaks loose, exposing the coarse aggregate underneath, you have a scaling problem. Scaling is most often caused by freezing, but inadequate air entrainment can also play a role.
Blisters
If the concrete finishing isn’t done correctly, air bubbles trapped in the concrete might push up to the airtight surface layer, resulting in blisters. While finish work might be to blame, including poor compacting, blisters could also be caused by poor-quality concrete. Bleed water could also cause blistering.
Popouts
A popout occurs when a small chunk of the surface concrete separates from the slab. In many cases, a chemical reaction between the aggregate and the cement is to blame. This reaction is called the Alkali-Silica Reaction (ASR). Popouts could also be caused by the expansion of unstable materials within the concrete mix.
But it’s no surprise that the expansion of water from freezing can also cause this problem. Popouts can happen at any time within the first year of service. Although unattractive, they don’t typically affect the strength of the concrete. ASR, however, will cause more serious problems if it’s widespread throughout the concrete.
Dusting
When fine powder develops on the top of concrete, we call it dusting. Most dusting is the result of floating bleed water back into the concrete’s surface. High water-to-cement ratios, poor curing, and surface freezing also contribute to dusting issues.
Discoloration
If your concrete has dark, splotchy, or striped marks, you’re seeing concrete discoloration. Again, water-to-cement ratios contribute to this common issue in residential concrete work. But the use of low-quality materials, hasty finishing, inconsistent mixtures, or even the use of calcium chloride could affect the consistency of your concrete’s color.
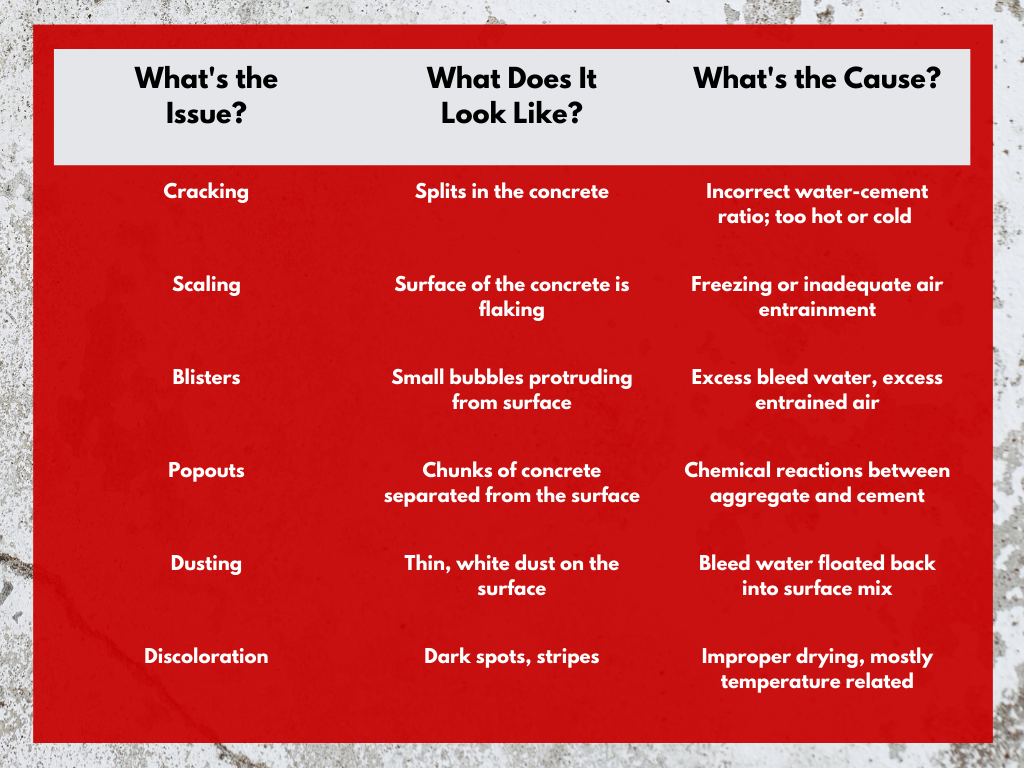
How Do You Prevent These Common Residential Concrete Issues?
Oddly enough, most of these common issues in residential concrete go back to poor water management. Curing time is another key factor, but moisture within the concrete’s components is often at fault for poor curing. So, if you can manage water correctly, you’ll be able to solve almost all of the problems contractors most commonly encounter.
Slow Concrete Pour
Ready-mix concrete has a limited timeframe from mixing to pouring and forming. If your crew isn’t ready within that first 90-minute timeframe, you’re going to see many of the most common issues in residential concrete listed above. That’s because ready-mix concrete begins to cure after 90 minutes. Some workers will add water on-site to keep it workable longer, but this move is a serious mistake.
It’s true that adding water to the concrete when it arrives will improve workability if the concrete has started to cure, but adding too much water will lead to weakened concrete. That extra water can also do some serious surface damage in the form of scaling, dusting, and cracking because that water likely won’t be mixed in properly.
If your job site is more than 90 minutes away, it is possible to transport concrete without problems. The supplier will adjust water-cement ratios and may include additives to slow the curing process until it’s on site. Just don’t try adding water to make up for waiting too long. Changing the water-cement ratio without proper calculations will only make your issues worse.
Water-Cement Ratio
More than any other factor, the water-cement ratio makes or breaks your concrete quality (quite literally). Portland cement, the “glue” of your concrete, is chemically reactive when hydrated. If there’s too much water, though, that cement won’t cure properly, leaving excess moisture in the concrete. If there’s too little water, the cement will never fully react, making the cement brittle.
The perfect balance between the water and the cement allows the concrete to dry and cure properly without leaving weak points between the aggregates. That standard ratio is 0.45 or less (a bit less than 1 part water to 2 parts cement). And at that ratio, you should be seeing a slump between 5 and 6 inches.
Incorrect Control Joints
Contractors that aren’t trained in concrete work will often misunderstand or improperly apply control joints to their slab work. The placement of your control joint changes with the dimensions and purposes of your slab, as well as a few other factors. It’s crucial that your joints are cut deep enough and placed close enough together to provide tensile stress relief as the concrete expands and contracts.
Again, water content within the slab plays a role in the amount of tensile stress your concrete will experience. Keep your water-cement ratio correct and your control joints will work properly.
Temperature Issues
Extreme heat and cold can cause issues with your concrete as well. When concrete is poured below 35°F, the curing process basically stops. Your cement won’t hydrate properly, leaving too little tensile and compressive strength to withstand its intended use.
Likewise, high temperatures change your concrete’s curing process. High temperatures result in faster evaporation. Water leaves the concrete too soon for the chemical reaction required to make the concrete strong. It also reduces the slump of the concrete, which can lead to workers adding more water to keep it workable. But that added water brings us back to the same problems we saw above.
The key to keeping your concrete strong in both extremes is to keep your temperatures stable. For cold curing, use heaters to keep the temperature of the slab above 35°F until the concrete reaches 500psi. For hot curing, use plastic covers, sun shades, or evaporation retardants to keep moisture trapped inside the concrete long enough for the cement to set properly.
Premature Finishing
Dusting and blisters are both connected to premature finishing. These common issues in residential concrete work, once again, connect directly to how water is managed in the mixture. Surface moisture from bleeding (when entrapped water seeps up through the concrete) must be dry before finish work starts. If bleed water is floated over the surface and mixed back in, you’ll see dusting.
Blisters also form when bleed water isn’t addressed properly. If concrete is too cold, too thick, or not properly vibrated, bleed water and entrained air can push up through the dried surface. Finishing before these processes are complete will leave your concrete susceptible to this type of damage.
Prevent blistering by allowing adequate curing time before adding impermeable finishing layers. Resist the urge to float bleed water back into the surface of the concrete, but instead, let it evaporate completely. You can also use concrete vibrators to encourage entrained air to come to the surface.
Inadequate Air Entrainment
Entrained (trapped) air in concrete serves a specific purpose. When excess water freezes in concrete, it creates tensile pressure. That added pressure needs to be displaced. The voids made by the entrained air provide that displacement. In climates with freeze-thaw cycles, air entrainment is especially important.
Keeping air entrainment between 5% and 8% in regions that experience freeze-thaw cycles will allow the concrete to respond to the expansion of moisture within the matrix. In climate-stable regions, air entrainment isn’t necessary for this function. However, in both climates, entrained air can make the concrete more workable while maintaining a higher water-to-cement ratio.
Best Practices for Residential Concrete Work
With all the most common issues in residential concrete, as well as some of the major mistakes contractors can make when working with concrete, let’s look at some of the basic requirements you’ll need to be familiar with to get your concrete right from the start.
Each purpose your concrete serves requires a different method to achieve your ideal strength and durability. Using the wrong methods could produce disastrous results. Here’s an outline of four common concrete projects you might encounter, and how you can avoid the most common issues in residential concrete work by maintaining appropriate standards for your concrete.
Garage Floors and Interior Floors
Most garage floors will need a 4-inch pour. While 2,500psi is the minimum in some codes, any concrete that you expect to use for parking vehicles or other heavy loads should be a minimum of 4,500psi. Any lower compressive strength will be susceptible to more rapid damage. Concrete slump should be 5 inches with a water-cement ratio of 0.5 or less.
Foundations, Driveways, Patios, Slabs, and Sidewalk
For these types of concrete structures, concrete must achieve 4,000psi after a 1-month cure, although the target strength should be 4,500psi or more when fully cured. Start with a 2-3” base of gravel, sand, limestone, or other aggregates. Pour pads, driveways, and sidewalks 4” deep, adding control joints about two to three times the depth of the poured concrete from each other (for a 4-inch pour, control joints should be spaced 8” to 12” apart across the entire slab).
Foundations for residential homes require 8-10” thickness and between 3,500psi and 4,000psi. Wood or metal frames, trenches, or insulated concrete forms should be used to shape the foundation correctly and provide enough support while it cures.
Concrete Countertops
Concrete countertops require a much thinner pour, between 1.5” and 2”, for the sake of decreasing overall weight. Concrete countertops need faster processing times to achieve higher early strength. High flexural strength helps with crack resistance, and low shrinkage is important to minimize curling.
Use stiff and hand-packed all-sand mixes for a smooth finish, and use vibration to eliminate any air bubbles under the surface. Polymer-based flowable mixes are also a smart choice for countertops, and cast-in-place settings are best for keeping the slab in a single piece.
Concrete Stairs
Of all the concrete projects listed, concrete stairs are the most difficult, as well as the most prone to the common issues in residential concrete work. Creating a nose for steps is especially difficult with concrete, but it isn’t a necessary component. Dry mixes work better to give the concrete extra strength and durability. It also allows the concrete to weather the freeze-thaw cycles better.
When to Hire a Professional
As you start your own residential projects, when should you look to concrete specialists instead of general contractors?
In our opinion, it should be every time.
Concrete’s unique chemistry and curing process makes it crucial to know how to keep the curing process controlled. Water management, water-cement ratio, and temperatures play key roles in achieving the required compressive strength and integrity of concrete. And without specific knowledge and training in the science of concrete, general contractors can do significant damage to your residential projects.
Brooks Construction is the Sioux Empire’s top choice for high-quality concrete pouring and finishing. We do general concrete construction like slabs, lots, foundations, and floors. But we also specialize in concrete finishing, including concrete dyeing, staining, and polishing. No matter what your project needs, Brooks is your single best source for concrete work in the region.
Schedule an appointment today to start working with us on your concrete construction projects. Our experts will make sure your concrete is engineered to meet your needs and last the tests of time and use!